A Basic Rundown of 3D Printing Technologies and Materials
This page is a helpful guide for 3D Printing Technologies and the types of parts you can produce in the different additive manufacturing techniques.
3D Printing Colorado can help you get parts produced in all of these materials and technologies. If you are unsure about what type of material or 3D Printing technology best fits your parts then give us a call at 303-466-0900 or email us at info@3dprintingcolorado.com – we can give you the information needed to make a confident choice for your 3D Printed parts.
Table of Contents
Fused Deposition Modeling (FDM) or Fused Filament Fabrication (FFF)
This is the most common, cheapest, and readily available form of 3D Printing.
Common Materials are:
PLA: one of the most commonly used filaments in 3D printing because it is so easy to use. PLA has minimal warping and shrinking compared to other materials, which means it thrives when making objects featuring flat surfaces and hard angles, or requiring tight tolerances for fit.
ABS: one of the most popular 3D printing materials in the world because it is strong, resilient, and offers a high degree of heat resistance. It’s a durable plastic that can be used for prototypes or functional / end use 3D printed parts.
Nylon: Flexibility meets strength with Nylon 3D Printing Filaments. It is stronger than PLA and ABS, it’s more chemically resistant and has a lower coefficient of friction than other filaments. Since objects printed in Nylon are so strong, sturdy, and flexible you can use it for End-use parts. Great for custom washers, wearing surfaces, wearing surfaces, and weight-bearing surfaces as well.
Flexable: Flex materials perform with an exciting combination of elongation, elasticity, and strength. Flex materials come in many colors that have a beautiful, strong sheen after being 3D printed. There are a few different durometers of flexi-material.
Common FDM & FFF Materials
Stereolithography (SLA)
Stereolithography is a form of 3D printing technology used for creating models, prototypes, patterns, and production of parts in a layer by layer fashion using photopolymerization, a process by which light causes chains of molecules to link, forming polymers.[1] Those polymers then make up the body of a three-dimensional solid.
SLA is used for Prototyping and Medical applications. Stereolithography is often used for prototyping parts for a relatively low price compared to traditional manufacturing. Stereolithography can produce accurate prototypes, even of irregular shapes. Businesses can use those prototypes to assess the design of their product or as publicity for the final product. Stereolithographic models have been used in medicine since the 1990s, for creating accurate 3D models of various anatomical regions of a patient, based on data from computer scans. SLA models are used as an aid to diagnosis, preoperative planning, and implant design and manufacture. This might involve for example planning and rehearsing osteotomies.
Color-Jet Printing (CJP)
ColorJet Printing (CJP) – An additive manufacturing technology which involves two major components – core and binder. The Core™ material is spread in thin layers over the build platform with a roller. After each layer is spread, a color binder is selectively jetted from inkjet print heads, which causes the core to solidify. The build platform lowers with every subsequent layer which is spread and printed, resulting in a full-color three-dimensional model. Whether printed with color or in standard white, parts can be additionally clear coated to add a hard, smooth coating or wax coated to smooth out the surface finish.
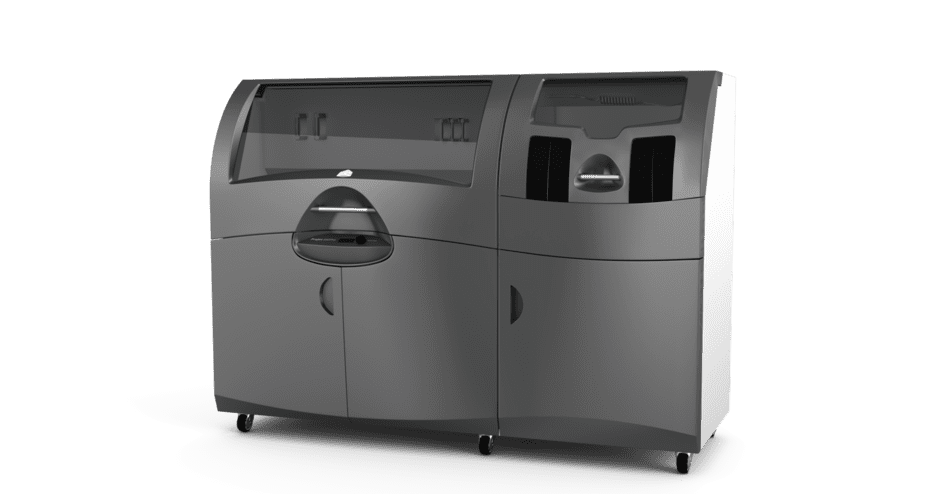
Materials used for ColorJet Printing: Core™ material – a gypsum based material
Common Uses: Engineering Prototypes, Full-color concept models, Architectural models, Demonstration models, Highly complex geometries, Quick production times
Multi-Jet Printing (MJP)
An inkjet printing process that uses piezo printhead technology to deposit either photocurable plastic resin or casting wax materials layer by layer. MJP is used to build Engineered parts, patterns, and molds with fine feature detail to address a wide range of applications. MJP printers offer the highest Z-direction resolution with layer thicknesses as low as 16 microns. MJP is a great choice for accuracy and True-to-CAD 3D Prints. The Multi-Jet family of printers are the most accurate 3D Printers on the market today.
ASTM Additive Manufacturing – 7 Tech Categories
- Vat Photopolymerisation – (SLA / DLP / CLIP)
- Material Jetting – (Multi/Poly Jet)
- Binder Jetting – (CJP, MJF)
- Material Extrusion – (FDM)
- Powder Bed Fusion – (SLS, DMLS)
- Directed Energy Deposition – (not in our wheelhouse)
- Sheet Lamination – (not in our wheelhouse)
Selective Laser Sintering (SLS)
Selective laser sintering (SLS) is an additive manufacturing (AM) technique that uses a laser as the power source to sinter powdered material (typically nylon or polyamide), aiming the laser automatically at points in space defined by a 3D model, binding the material together to create a solid structure. It is similar to selective laser melting; the two are instantiations of the same concept but differ in technical details. SLS (as well as the other mentioned AM techniques) is a relatively new technology that so far has mainly been used for rapid prototyping and for low-volume production of component parts.
PostPro3D Vapor Smoothing
PostPro Chemical Vapor Smoothing process is a physio-chemical process that can smooth a wide variety of thermoplastic polymers. The process is non-line-of-sight and can smooth complex internal cavities of polymer parts. PostPro vapor smoothing technology is highly controllable, allowing reproducible results with no degradation of a parts’ mechanical properties. The process has been evolved from the PUSH process, developed at the University of Sheffield.
-
PostPro3D Smoothed -
PostPro3D Smoothed -
PostPro3D Smoothed -
No PostPro3D Smoothed
Multi Jet Fusion (MJF)
Multi Jet Fusion (MJF) is a powder-bed 3D printing process developed by HP that bonds agent and powder in a process similar to binder jetting. Unlike point-by-point laser-based powder-bed fusion systems, MJF selectively distributes fusing and detailing agents across a bed of powder, and layers are fused together using infrared light.
The Multi Jet Fusion system consists of exchangeable build units that can be wheeled between MJF 3D printers and separate postprocessing stations for rapid cooldown and powder removal. This modular system allows the printer and postprocessing stations to run continuously while build units cycle through, speeding part production.
-
Multi Jet Fusion -
Multi Jet Fusion -
Multi Jet Fusion -
Multi Jet Fusion